Product Description
ZheJiang E-Rally Technology Co., Ltd. is 1 of most experienced professional rapid prototype and mass production manufacturer. Located in ZheJiang China.
Our market focus is to supply the professional machining solution for micro precision parts, Auto Spare Parts, Especially Semiconductor equipment parts, Environmental protection equipment parts, Testing equipment parts, And other kinds of high precision parts manufacturing. We don’t only provide OEM services, we can also provide you with the professional technical support and best production plan of equipment and parts.
We specialize in rapid prototyping, rapid tooling, low volume and mass production manufacturing of custom parts. We produce over 10,000 kinds of parts every year, with rich processing experience, we can make everything into reality. Short lead time, 24-hour response, full steps QC inspection, Non-disclosure agreement is strictly respected.
Please feel free to contact us.
Cooperate with us You Will Get:
* Competitive Price Of CNC Precision Machinery part
* Good Quality Assurance
* In Time Sampling & In Time Shipment
* Quality Guarantee
* Free Sample Can Be Provided Some Time
* Low MOQ
* Reply in 24 hours and fast quotaion
How to work with us?
1. Send us your 3D drawing (STEP/IGS/SolidWorks format etc. ) so we can check all dimension to quote.
2. Expatiate your requirements (your quantity, material, and surface finish requirements, etc.) to our email
Drawing Format Can Done By E-Rally?
dwg, dxf, prt, iGS, step, stp, iges, slprt, asm, x_t files are all accepted.
What kinds of CNC machining product is suitable to send to E-Rally for quoation?
CNC machining product, CNC milling product, CNC lathing product, CNC turning product, CNC precision machining product, maching product, precision product and all machining parts used in different industrials such as: spray nozzle, car accessories, railway accessories, bathroom accessoires, equipemnt spare parts, pipe and fittings and so on.
Product Name: |
CNC Machinery Part For Multi industry equipment Auto Part Phone Parts Machine Part Household appliance parts |
Manufacture Process: |
Design – Primary Processing-CNC Machining-Inspecting-Packing |
Main Material: |
Aluminium,Brass,Steel,etc. |
Color: |
Custom Color |
Finish: |
Clean/Polish/Anodized/Custom Surface |
Production Equipment: |
CNC Machining, CNC Turning, CNC Milling, Complex CNC turning & milling, 4 & 5 Axis CNC Machining, Laser Cutting, CNC Bending, Wire Cutting, Stamping, Casting, Grinding etc. |
Surface Treatment: |
Clear/black/golden/blue/red/hard Anodizing Glass bead blasting, Brushing, Polish Zinc/Nickel/Silver Plating Powder Coating, Heat treatment, Black oxdized Passivate, Painting, Laser engraving, Silk screen etc. |
Measuring Instruments and Equipment: |
1) Micrometer
2) Smooth plug gauge
3) Thread gauge
4) Image measuring instrument
5) Coordinate Measuring Machine
6) Roughness tester
7) Routine inspection of calipers
|
Tolerance: |
± 0.005~0.100 mm |
Quality control: |
ISO 9001:2008 & IATF 16949 |
Sample time: |
1-3 days |
Service: |
Customized OEM/ODM |
Shipment: |
Fedex, DHL, UPS, Sea or Air Shipment, etc. |
One-stop Service: |
Custom Design, Fabrication, Assembly And Delivery |
File Format: |
Solidworks,Pro/Engineer,Auto CAD,C4D,Creo,PDF,JPG,DXF,IGS,STEP,DWG |
Customized CNC Parts for Various Equipment Auto Moto Parts
High precision custom mold / Injection CZPT / Mold accessories
Machinable materials |
Steel |
1018 |
Stainless Steel |
17-4PH |
Copper/Brass |
110 |
1045 |
302 |
145 |
1050 |
303 |
147 |
1117 |
304 |
314 |
1141 |
316 |
316 |
1144 |
321 |
360 |
11L17 |
409 |
544 |
11L41 |
410 |
624 |
1215 |
416 |
Beryllium Copper |
12L14 |
420 |
Plastics |
ABS |
4140 |
430 |
PC |
4142 |
440 |
PP |
41L40 |
Aluminum |
2011 |
PEEK |
41L42 |
2571 |
PET |
8620 |
5052 |
PUM |
86L20 |
6061 |
PVC |
E52100 |
6063 |
Delron |
Fatigue proof |
6082 |
Nylon |
Stress proof |
6262 |
Teflon |
Customized |
7075 |
Celcon |
Steel |
Aluminum |
Copper/Brass |
Plastics |
CNC Machining |
CNC Turning |
Motorcycles Parts |
Mould |
Laser Cutting |
Stamping Parts |
☆☆☆☆☆
All the pictures are actually taken by rally. Every year, more than 10,000 kinds of parts are manufactured, involving many industries:
Medical equipment |
Semiconductor equipment |
5g communication equipment |
Packaging equipment |
Intelligent assembly |
1. Are you a trader or a manufacturer?
KTS:We are manufacturer, our factory is located in HangZhou, ZheJiang Province, China, The starting point of HangZhou Europe Railway, Welcome to visit our factory.
2. May i order small quantity of CNC mashinery parts or carbide products?
KTS:We support small batch customization, but different models have different MOQ, please contact US to confirm.
3.Can you provide sample?
KTS: Yes, please feel free to tell us, also your own design is welcome to make sample for you, After confirming the authenticity of your company, we are willing to provide small quantities of free samples.
4.What is your price term, payment term and delivery terms?
Price Terms: By FOB ZheJiang or other port. Balance before shipment. Rail transport is also allowed.
Payment Terms: T/T advance.
Delivery Terms: By express, by air, by train, by shipment or as requirement
Contact us:
ZheJiang E-Rally supply Chain Machinery Co.,Ltd.
Address: No.1, floor 1, building 1, No.26 Xixin Avenue, high tech Zone, HangZhou, ZheJiang , China
If there’s anything we can help, please feel free to contact with us.
We’re sure your any inquiry or requirement will get prompt attention.
Screw Sizes and Their Uses
Screws have different sizes and features. This article will discuss screw sizes and their uses. There are 2 main types: right-handed and left-handed screw shafts. Each screw features a point that drills into the object. Flat tipped screws, on the other hand, need a pre-drilled hole. These screw sizes are determined by the major and minor diameters. To determine which size of screw you need, measure the diameter of the hole and the screw bolt’s thread depth.
The major diameter of a screw shaft
The major diameter of a screw shaft is the distance from the outer edge of the thread on 1 side to the tip of the other. The minor diameter is the inner smooth part of the screw shaft. The major diameter of a screw is typically between 2 and 16 inches. A screw with a pointy tip has a smaller major diameter than 1 without. In addition, a screw with a larger major diameter will have a wider head and drive.
The thread of a screw is usually characterized by its pitch and angle of engagement. The pitch is the angle formed by the helix of a thread, while the crest forms the surface of the thread corresponding to the major diameter of the screw. The pitch angle is the angle between the gear axis and the pitch surface. Screws without self-locking threads have multiple starts, or helical threads.
The pitch is a crucial component of a screw’s threading system. Pitch is the distance from a given thread point to the corresponding point of the next thread on the same shaft. The pitch line is 1 element of pitch diameter. The pitch line, or lead, is a crucial dimension for the thread of a screw, as it controls the amount of thread that will advance during a single turn.
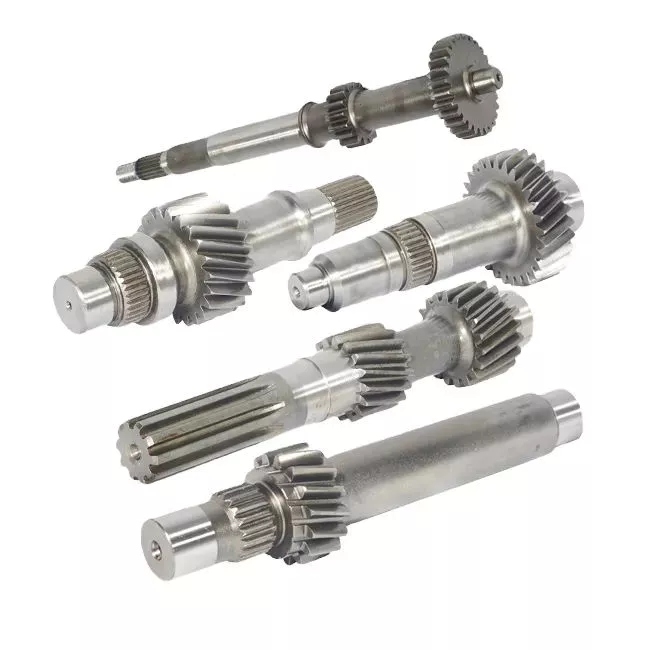
The pitch diameter of a screw shaft
When choosing the appropriate screw, it is important to know its pitch diameter and pitch line. The pitch line designates the distance between adjacent thread sides. The pitch diameter is also known as the mean area of the screw shaft. Both of these dimensions are important when choosing the correct screw. A screw with a pitch of 1/8 will have a mechanical advantage of 6.3. For more information, consult an application engineer at Roton.
The pitch diameter of a screw shaft is measured as the distance between the crest and the root of the thread. Threads that are too long or too short will not fit together in an assembly. To measure pitch, use a measuring tool with a metric scale. If the pitch is too small, it will cause the screw to loosen or get stuck. Increasing the pitch will prevent this problem. As a result, screw diameter is critical.
The pitch diameter of a screw shaft is measured from the crest of 1 thread to the corresponding point on the next thread. Measurement is made from 1 thread to another, which is then measured using the pitch. Alternatively, the pitch diameter can be approximated by averaging the major and minor diameters. In most cases, the pitch diameter of a screw shaft is equal to the difference between the two.
The thread depth of a screw shaft
Often referred to as the major diameter, the thread depth is the outermost diameter of the screw. To measure the thread depth of a screw, use a steel rule, micrometer, or caliper. In general, the first number in the thread designation indicates the major diameter of the thread. If a section of the screw is worn, the thread depth will be smaller, and vice versa. Therefore, it is good practice to measure the section of the screw that receives the least amount of use.
In screw manufacturing, the thread depth is measured from the crest of the screw to the root. The pitch diameter is halfway between the major and minor diameters. The lead diameter represents the amount of linear distance traveled in 1 revolution. As the lead increases, the load capacity decreases. This measurement is primarily used in the construction of screws. However, it should not be used for precision machines. The thread depth of a screw shaft is essential for achieving accurate screw installation.
To measure the thread depth of a screw shaft, the manufacturer must first determine how much material the thread is exposed to. If the thread is exposed to side loads, it can cause the nut to wedge. Because the nut will be side loaded, its thread flanks will contact the nut. The less clearance between the nut and the screw, the lower the clearance between the nut and the screw. However, if the thread is centralized, there is no risk of the nut wedgeing.

The lead of a screw shaft
Pitch and lead are 2 measurements of a screw’s linear distance per turn. They’re often used interchangeably, but their definitions are not the same. The difference between them lies in the axial distance between adjacent threads. For single-start screws, the pitch is equal to the lead, while the lead of a multi-start screw is greater than the pitch. This difference is often referred to as backlash.
There are 2 ways to calculate the pitch and lead of a screw. For single-start screws, the lead and pitch are equal. Multiple-start screws, on the other hand, have multiple starts. The pitch of a multiple-start screw is the same as its lead, but with 2 or more threads running the length of the screw shaft. A square-thread screw is a better choice in applications requiring high load-bearing capacity and minimal friction losses.
The PV curve defines the safe operating limits of lead screw assemblies. It describes the inverse relationship between contact surface pressure and sliding velocity. As the load increases, the lead screw assembly must slow down in order to prevent irreversible damage from frictional heat. Furthermore, a lead screw assembly with a polymer nut must reduce rpm as the load increases. The more speed, the lower the load capacity. But, the PV factor must be below the maximum allowed value of the material used to make the screw shaft.
The thread angle of a screw shaft
The angle between the axes of a thread and the helix of a thread is called the thread angle. A unified thread has a 60-degree angle in all directions. Screws can have either a tapped hole or a captive screw. The screw pitch is measured in millimeters (mm) and is usually equal to the screw major diameter. In most cases, the thread angle will be equal to 60-degrees.
Screws with different angles have various degrees of thread. Originally, this was a problem because of the inconsistency in the threading. However, Sellers’s thread was easier to manufacture and was soon adopted as a standard throughout the United States. The United States government began to adopt this thread standard in the mid-1800s, and several influential corporations in the railroad industry endorsed it. The resulting standard is called the United States Standard thread, and it became part of the ASA’s Vol. 1 publication.
There are 2 types of screw threads: coarse and fine. The latter is easier to tighten and achieves tension at lower torques. On the other hand, the coarse thread is deeper than the fine one, making it easier to apply torque to the screw. The thread angle of a screw shaft will vary from bolt to bolt, but they will both fit in the same screw. This makes it easier to select the correct screw.
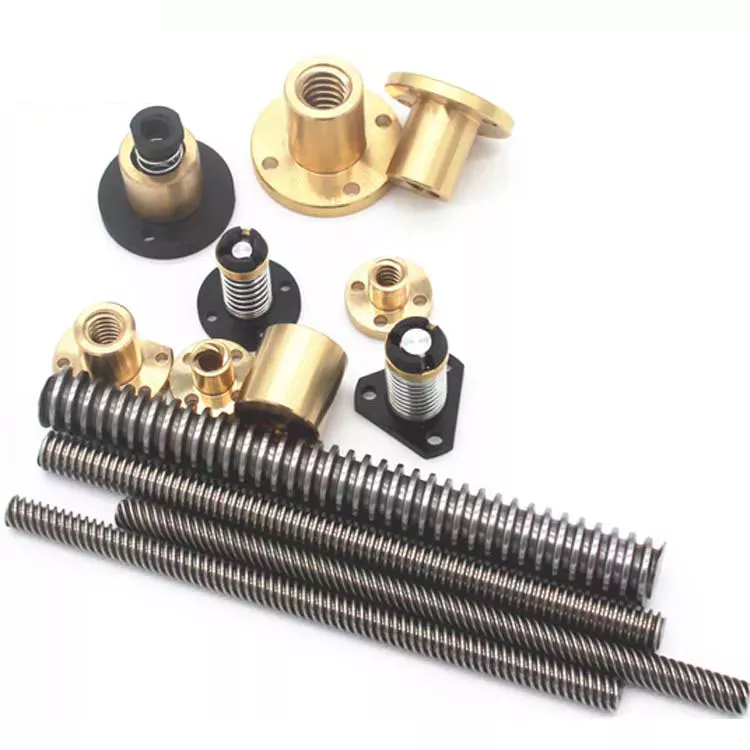
The tapped hole (or nut) into which the screw fits
A screw can be re-threaded without having to replace it altogether. The process is different than that of a standard bolt, because it requires threading and tapping. The size of a screw is typically specified by its major and minor diameters, which is the inside distance between threads. The thread pitch, which is the distance between each thread, is also specified. Thread pitch is often expressed in threads per inch.
Screws and bolts have different thread pitches. A coarse thread has fewer threads per inch and a longer distance between threads. It is therefore larger in diameter and longer than the material it is screwed into. A coarse thread is often designated with an “A” or “B” letter. The latter is generally used in smaller-scale metalworking applications. The class of threading is called a “threaded hole” and is designated by a letter.
A tapped hole is often a complication. There is a wide range of variations between the sizes of threaded holes and nut threads, so the tapped hole is a critical dimension in many applications. However, even if you choose a threaded screw that meets the requisite tolerance, there may be a mismatch in the thread pitch. This can prevent the screw from freely rotating.

